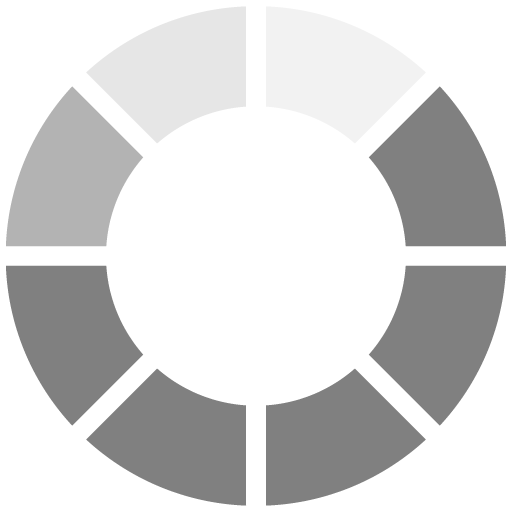
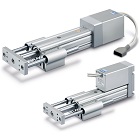
LE2YG, High Performance Guide Rod for Manifold Controller
LE2YG guide rod actuator pairs an LE2Y actuator with a bolt-on bearing block with double guide rods. Guide selection offers either slide or ball bushing bearings. The motor is upgraded with higher performance and a batteryless absolute encoder. Work load ratings, pushing force, speed, acceleration and power consumption are improved. Motor orientation can be reverse mounted on top for compact length, or inline for compact height. A high speed ballscrew lead is available on sizes 25 and 32. LE2 actuators are compatible with the JXC1-M manifold controller, with a different cable connector and no compatibility with JXC controllers. The JXD1-M manifold controller can detect the actuator type, size and stroke when connected. The controller and cables are ordered separately, simplifying the part number.
- Body sizes: 16, 25, 32
- Maximum work load: 100 kg (horizontal); 44 kg (vertical)
- Maximum speed: 900 mm/s (24mm lead, size 32)
- Maximum acceleration: 10,000 mm/s² (horizontal); 5,000 mm/s² (vertical)
- Stroke range: 30 to 300mm in 50mm increments
- Positioning repeatability: ±0.02mm
- Motor type: 24 VDC step motor with absolute batteryless encoder
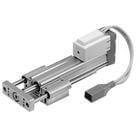
LEYG Guided Rod, Incremental Encoder
- Same features and performance as standard LEY, plus:
- Maximum stroke: 300 mm
- Bearing types: sliding bushings or ball bushing bearings
- Maximum allowable rotational torque: 5.76 N•m (sizes 32, 40; stroke dependent)
- Non-rotating accuracy of plate: ±0.05° (slide bearing); ±0.06° (ball bushing bearing)
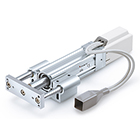
LEYG Guided Rod, Battery-less Absolute Encoder
The LEYG guided rod electric actuator pairs a LEY actuator with a bolt-on bearing block with double guide rods. The guide rods counter rotational forces instead of the drive and motor, and also resist shock and sustained lateral loads. Guide selection offers either slide or ball bushing bearings. The motor orientation can be reverse mounted on top for compact length, or inline for compact height. This version includes a 24VDC motor with a battery-less absolute encoder. This encoder allows the actuator to be powered down without losing its positional awareness. The machine's PLC can access the controller's operational and positional step data through several fieldbus protocols, IO-Link, or parallel I/O.
- Body sizes: 16, 25, 32, 40
- Maximum work load: 90 kg (horizontal; 51 kg (vertical)
- Maximum pushing force: 1058 N
- Maximum speed: 500 mm/s
- Maximum stroke: 300mm
- Positioning repeatability: ±0.02mm
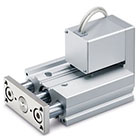
LEG, High Rigidity Guide Rod, High Performance, Battery-less Absolute Encoder
LEG is a rod actuator featuring a guide body with two guide rods and a front tool plate. This is the electric version of our well-known MGP pneumatic guided actuator. Guide rod diameters and bushings are larger than those available in the LEYG, offering improved rigidity. The guide rods stabilize the actuator and support offset loads, making LEG suitable as a conveyor stopper, or for lifting or pushing larger objects. The compact extruded body also has grooves for mounting external position sensors. The 24VDC motor includes a battery-less absolute encoder, allowing the actuator to be powered down without losing its positional awareness. Replacement battery inventory and end-of-life recycling efforts are no longer necessary. Motor operation is provided by the JXC*H High Performance controller line, with either PLC or Ethernet fieldbus protocol interfaces.
- Body sizes: 25, 32, 40
- Maximum work load: 60 kg (horizontal); 27 kg (vertical) (size 40)
- Maximum pushing force: 553 N (size 40)
- Maximum speed: 250 mm/s (size 25)
- Maximum stroke: 100mm
- Positioning repeatability: ±0.02mm